Exploring the World of Plastics Injection Molding
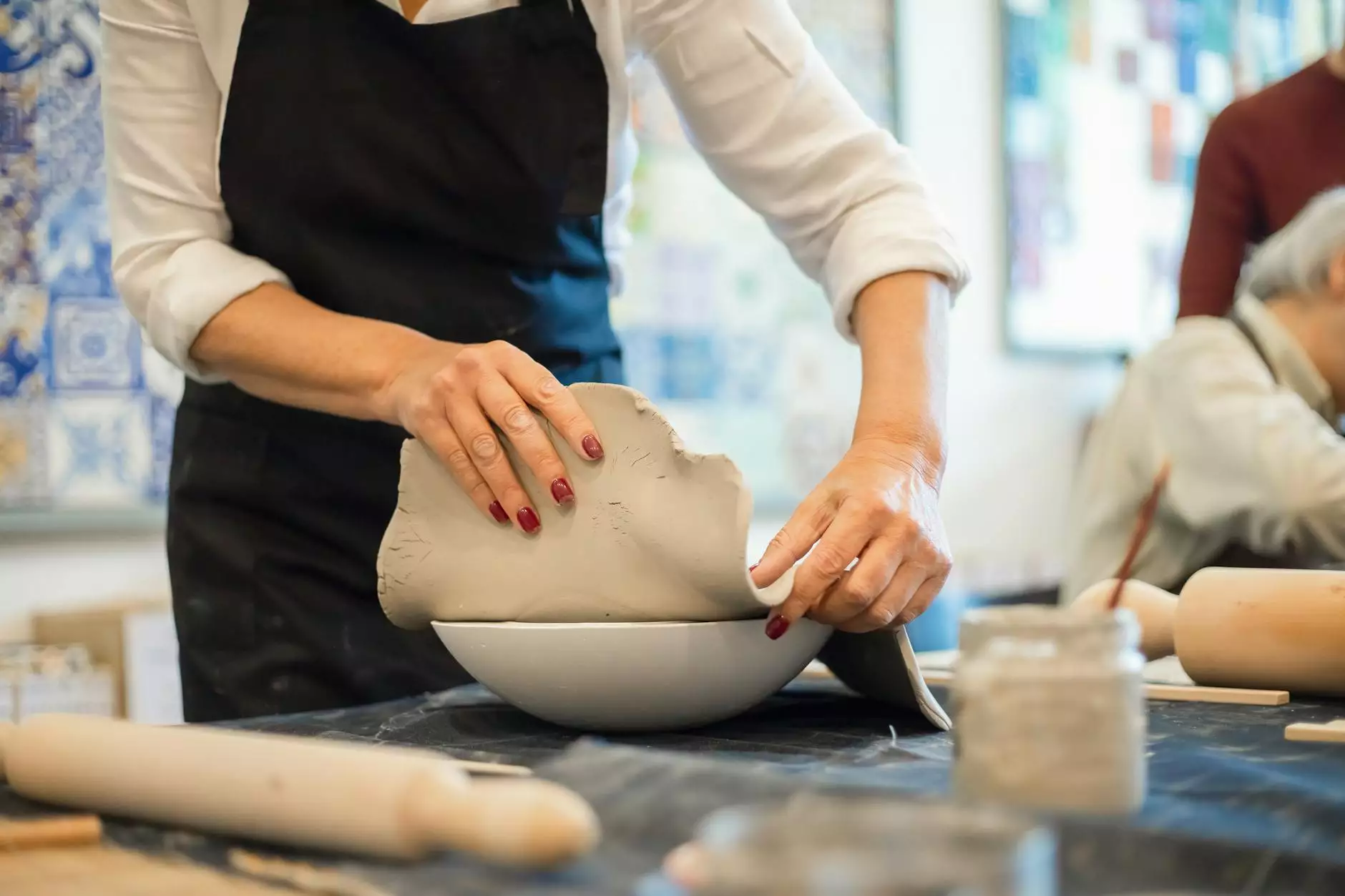
Plastics injection molding is a cutting-edge manufacturing process that has revolutionized the way we produce plastic components. This process involves injecting molten plastic into a mold to create intricate parts with high precision. With its extensive applications across various industries, understanding the intricacies of this method can significantly benefit businesses looking to enhance their production capabilities.
Understanding the Basics of Plastics Injection Molding
At its core, plastics injection molding is a manufacturing technique that allows for the creation of large volumes of identical parts. This method begins with the melting of plastic pellets, which are then injected into a specially designed mold. Once the plastic cools and hardens, the mold is opened, and the final product is ejected.
The Injection Molding Process
The following steps outline the typical plastics injection molding process:
- Material Preparation: This involves drying the resin to remove moisture, ensuring that the final product has optimal properties.
- Injection: The dried resin is heated until it becomes molten and is then injected into the mold under high pressure.
- Cooling: The injected plastic cools within the mold, allowing it to take on the desired shape.
- Part Ejection: Once cooled and solidified, the mold is opened, and the finished product is ejected.
- Trimming: Any excess material, known as flash, is removed for a clean finish.
Benefits of Plastics Injection Molding
Choosing to incorporate plastics injection molding has numerous advantages for manufacturers. Here are some key benefits:
- Efficiency: The process allows for rapid production rates, making it ideal for mass manufacturing.
- Consistency: High levels of precision ensure that each part produced is uniform and fits within tight tolerances.
- Material Versatility: A wide variety of thermoplastics and thermosetting polymers can be used, allowing for customized solutions.
- Cost-Effectiveness: While initial setup costs can be high, the long-term savings from mass production make it economically viable.
- Complex Designs: Intricate shapes and more complex designs are achievable, which can enhance product functionality.
Applications of Plastics Injection Molding
The applications for plastics injection molding are almost limitless. Here are some of the key industries that utilize this method:
Automotive Industry
In the automotive sector, components such as dashboards, panels, and even intricate parts like connectors are produced using plastics injection molding. The lightweight nature of plastics contributes to fuel efficiency and design flexibility.
Consumer Products
From kitchen utensils to electronic housings and toys, consumer goods heavily rely on this manufacturing method to achieve cost-effective and high-volume production.
Medical Devices
The medical field requires highly sterile, precise, and reliable plastic components. Injection molding delivers the quality and consistency required for medical devices and supplies.
Electronics
Many electronic devices incorporate plastic enclosures, connectors, and components, all produced through plastics injection molding to ensure durability and safety.
The Future of Plastics Injection Molding
As technology continues to advance, so too does plastics injection molding. Innovations such as the use of 3D printing for mold design, automation in production lines, and advancements in materials science are set to improve efficiency and increase the sustainability of the process.
Moreover, with the growing awareness of environmental issues, the development of biodegradable plastics and recycled materials for injection molding is becoming a focal point, ensuring that this manufacturing method adapts to meet future sustainability goals.
Challenges in Plastics Injection Molding
While there are numerous benefits, it is also important to recognize the challenges that come with plastics injection molding:
- Initial Cost: The investment in machinery and mold design can be significant, particularly for custom molds.
- Material Limitations: Not all plastics are suitable for injection molding, and the material choice affects the final product's properties.
- Complexity of Mold Design: Creating a mold that properly captures intricate designs can be a complex and time-consuming process.
Conclusion
In conclusion, plastics injection molding is a vital manufacturing process that delivers numerous benefits across various industries. Understanding its operation, advantages, and future potential can help businesses optimize their production lines and improve product offerings. Whether you are in the automotive, medical, or consumer product sector, leveraging the capabilities of plastics injection molding can lead to significant advancements in efficiency and product quality.
For businesses interested in plastics injection molding, partnering with experienced metal fabricators like Deepmould.net can provide you with the expertise needed to navigate the complexities of this process. In this dynamic manufacturing landscape, staying informed and adapting to newer technologies will be key to maintaining a competitive edge.