The Rise of Prefabricated Buildings: Transforming the Construction Industry
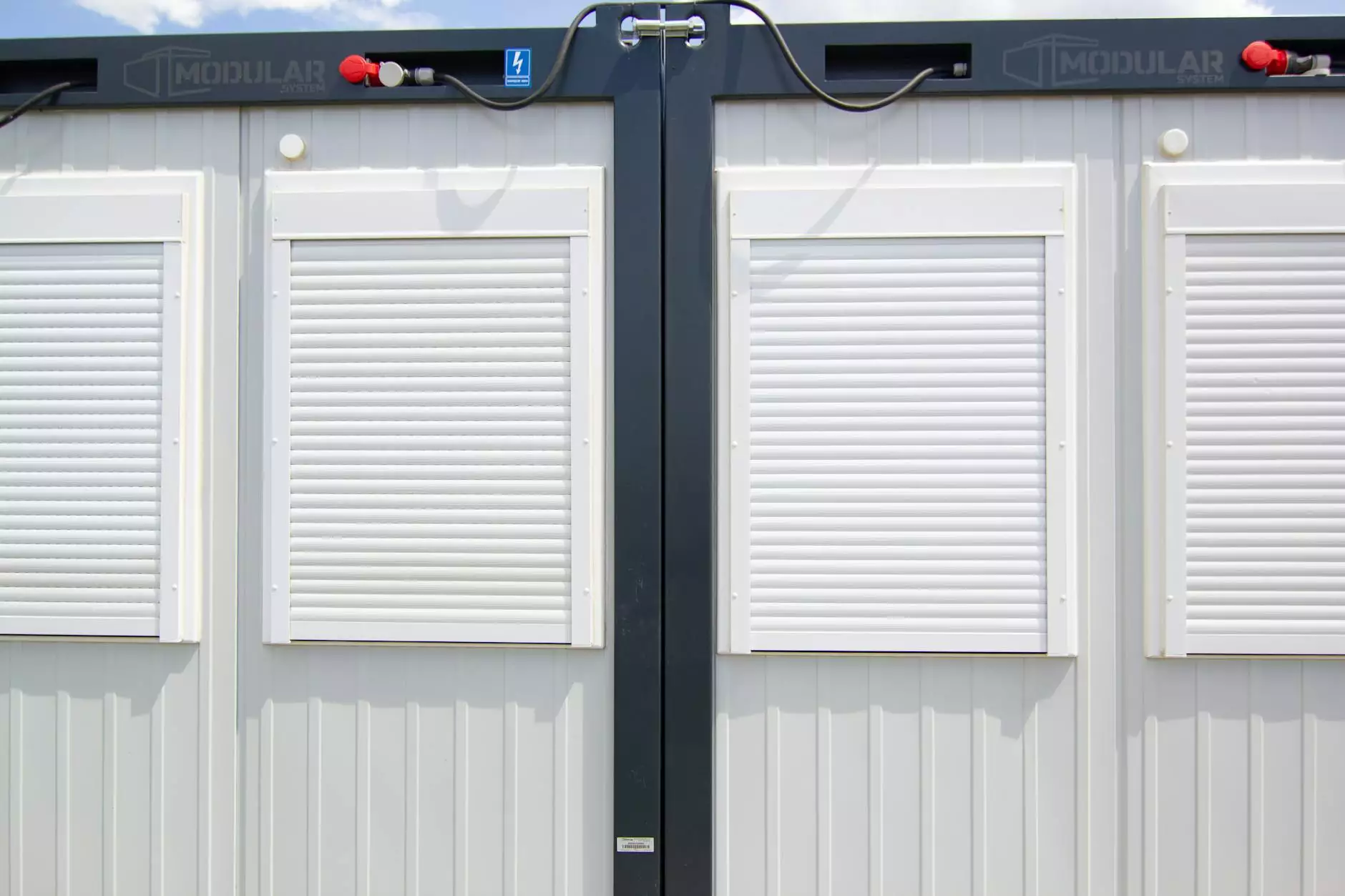
The construction industry is undergoing a significant transformation as it embraces modern techniques and technologies. One such innovative approach that stands out is the advent of prefabricated buildings. These structures, built off-site and assembled on-location, not only enhance efficiency but also offer remarkable advantages in both time and cost savings. In this article, we explore the multifaceted benefits of prefabricated buildings, how they are reshaping the construction landscape, and the future they promise for contractors and businesses alike.
Understanding Prefabricated Buildings
Prefabricated buildings are structures that are constructed using factory-made components. These components are produced in a controlled environment where precision and quality control can be maintained. Once these elements are manufactured, they are transported to the construction site and assembled to form a complete building. This process contrasts sharply with traditional construction methods that rely heavily on on-site labor and variable weather conditions.
Benefits of Prefabricated Buildings
1. Time Efficiency
One of the foremost benefits of prefabricated buildings is the reduction in construction time. Traditional construction methods can take weeks or months to complete, depending on the complexity of the project. In contrast, the assembly of prefabricated components can occur in a matter of days or weeks, significantly accelerating the overall project timeline. This rapid turnaround is especially advantageous for contractors and developers who are keen to reduce waiting times.
2. Cost Savings
Cost efficiency is a priority for any construction project. By utilizing prefabricated buildings, contractors can save money in several key areas:
- Reduced Labor Costs: With less time spent on-site, the overall labor costs decrease.
- Material Waste Reduction: Prefabrication minimizes waste as components are precisely manufactured to specifications.
- Lower Site Preparation Costs: Fewer on-site disturbances translate to lower costs for land preparation and management.
3. Quality Control
When components are built in a factory, it is easier to maintain high standards of quality. Prefabricated buildings undergo stringent quality control measures during production, ensuring that every part meets and exceeds necessary building codes. This consistent quality helps mitigate problems that might arise in traditional on-site construction, such as weather delays or human error.
4. Sustainability
As the world becomes more environmentally conscious, sustainability in construction has taken center stage. Prefabricated buildings align with these sustainable practices in multiple ways:
- Eco-friendly Materials: Many prefabricated structures utilize renewable resources or recycled materials.
- Energy Efficiency: Improved insulation and ventilation in factory-made components reduce energy consumption.
- Less On-Site Waste: Efficient use of materials during manufacturing leads to less waste generated on-site.
5. Design Flexibility
Contrary to the misconception that prefabricated buildings are limited in design, these structures can be remarkably versatile. From modular designs to customized layouts, prefabricated construction allows for a wide range of architectural styles and options. Contractors can access endless designs that cater to the specific needs of their clients, ensuring that no two buildings have to look alike.
Applications of Prefabricated Buildings
Prefabricated buildings have found their niche in various sectors, showcasing their adaptability and functionality.
1. Residential Construction
The residential sector has significantly benefited from the prefabricated building approach. Homebuilders are now able to construct homes faster without compromising on quality. Whether it's a single-family home or a multi-family residence, prefabricated options simplify the building process, making homeownership more accessible.
2. Commercial Buildings
In the commercial realm, prefabricated buildings are increasingly being utilized for offices, retail spaces, and even restaurants. Their speed of construction and cost-effectiveness makes them an attractive option for business owners looking to establish operations rapidly.
3. Infrastructure and Urban Development
Local governments and municipalities have begun turning to prefabrication for infrastructure projects. Schools, hospitals, and public facilities can be erected quickly and affordably, addressing urgent community needs without lengthy delays.
4. Industrial Applications
Many industries, including construction and logistics, are adopting prefabricated buildings for warehouses and factories. These structures can be designed to accommodate specific operational requirements, leading to improved efficiency and productivity.
The Process of Prefabrication
Understanding the process of creating prefabricated buildings can provide insights into why they are so advantageous. The typical lifecycle includes the following stages:
1. Design and Planning
Collaboration between architects, engineers, and contractors is crucial during the design phase. Advanced software applications are often used to create precise blueprints, allowing for customization and ensuring that every aspect meets the expected standards.
2. Manufacturing
Once the designs are finalized, the components are manufactured in a controlled environment. This includes not only structural elements but also finishes, electrical, and plumbing systems, all integrated into the factory-produced modules.
3. Transportation
The fully manufactured components are then transported to the construction site. Careful logistics planning is critical at this stage to ensure that delivery aligns seamlessly with the assembly schedule.
4. Assembly on Site
At the construction site, skilled labor teams are tasked with the assembly of the prefabricated elements. This process is significantly quicker than traditional methods and often results in a safer work environment due to reduced on-site activity.
Challenges and Considerations
While prefabricated buildings offer numerous advantages, there are a few challenges and considerations that stakeholders should keep in mind:
- Transport Limitations: The size and weight of prefabricated components can create logistical issues during transport.
- Site Preparation: While prefabricated assembly reduces on-site construction time, proper site preparation is still crucial for successful installation.
- Regulatory Hurdles: Varying building codes and regulations can complicate the adoption of prefabricated methods in certain regions.
The Future of Prefabricated Buildings
The future of prefabricated buildings appears promising as construction technology continues to evolve. Innovations such as 3D printing, advanced materials, and robotics are on the horizon, poised to further streamline the prefabrication process. As sustainability becomes a cornerstone of modern construction, the prefabrication industry will likely expand to incorporate even more eco-friendly practices, paving the way for a greener future.
Conclusion
In conclusion, prefabricated buildings represent a significant advancement in the construction industry, delivering time efficiency, cost savings, and sustainability. For contractors and businesses in the construction sector, adopting prefabrication can lead to enhanced operational efficiency and improved project outcomes. As this innovative approach gains traction, it is clear that prefab construction is not just a trend, but a transformative movement that will shape the future of building. To explore the possibilities of prefabricated construction for your next project, visit module-t.com and discover how to leverage this cutting-edge technology.